Try Statistical Software for Free
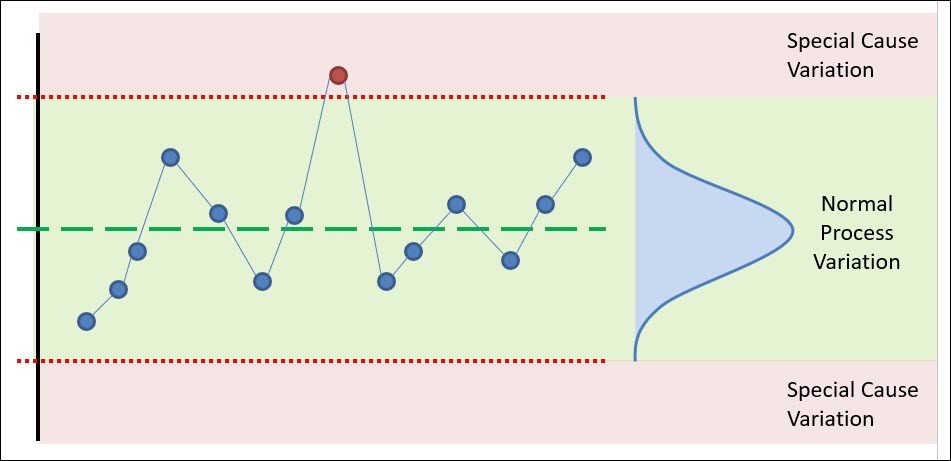
What is SPC / Statistical Process Control?
Statistical process control (SPC) is a method used to monitor and control a process by using statistical analysis. It involves collecting data about a process, analyzing the data using statistical tools, and using the results to identify any deviations from the expected performance of the process. This allows manufacturers to identify and correct problems before they result in defective products.
Here are the main steps involved in statistical process control:
- Define the process: Identify the process that you want to control and define its key characteristics, such as output, inputs, and any other relevant factors.
- Collect data: Gather data about the process, such as measurements of output, inputs, and other relevant factors. This data is typically collected over time, allowing you to see how the process is performing over time.
- Analyze the data: Use statistical tools, such as control charts, to analyze the data and identify any deviations from the expected performance of the process.
- Identify and correct problems: If deviations are found, try to identify the cause of the problem and implement corrective actions to bring the process back into control.
By following these steps, manufacturers can identify and correct problems in their processes, resulting in improved quality and increased efficiency.
Additional details about statistical process control:
- SPC can be applied to any process where data can be collected, including manufacturing processes, service processes, and administrative processes.
- SPC involves setting limits or targets for the process and monitoring the process to ensure that it stays within these limits. This helps to ensure that the process is stable and producing consistent results.
- SPC can be used to identify both common causes of variation (caused by the inherent nature of the process) and special causes of variation (caused by external factors such as equipment malfunction or operator error). By identifying and correcting special causes, manufacturers can reduce the overall variability of the process.
- SPC requires a commitment to continuous improvement, as it involves ongoing data collection and analysis to identify and correct problems.
- Some of the tools commonly used in SPC include control charts, which plot the data collected from a process over time and show the expected limits of the process; cause-and-effect diagrams, which help to identify the root causes of problems; and process capability indices, which compare the performance of a process to the specifications or requirements for the product being produced.
Difference between SPC and trend analysis.
Trend analysis is a method of analyzing data over time to identify patterns and trends. It involves collecting data about a particular variable or group of variables, and analyzing the data to identify any patterns or trends that may exist. Trend analysis can be used to identify long-term trends, such as changes in customer behavior or market trends, or short-term trends, such as changes in production efficiency.
Statistical process control (SPC) is a method used to monitor and control a process by using statistical analysis. It involves collecting data about a process, analyzing the data using statistical tools, and using the results to identify any deviations from the expected performance of the process. SPC is typically used to identify and correct problems in a process, rather than to identify trends.
While both trend analysis and SPC involve the use of statistical tools to analyze data, they are used for different purposes and focus on different aspects of the data. Trend analysis is used to identify patterns and trends in data over time, while SPC is used to monitor and control a process by identifying deviations from the expected performance of the process.