Zometric Supplier Quality Management Software
A Robust, Comprehensive Approach to Supplier Quality Management on an Enterprise Scale
Supplier Quality Management : A Comprehensive Approach to Ensure Supplier Quality Across the Organization
In the ever-evolving landscape of the manufacturing industry, quality is non-negotiable. The success of your products and your reputation hinge on the quality of the materials and components used in production. That's where Zometric's Supplier Quality Management Software comes in – a game-changer for manufacturers seeking excellence in supplier management.
Supplier Quality Management Software Solutions
CONTINUOUS MANUFACTURING
BATCH MANUFACTURING
DISCRETE MANUFACTURING
JOB WORK MANUFACTURING
Why Choose Zometric's Supplier Quality Management Software?
Zometric: The Ultimate Supplier Quality Management System for Your Business.
Key Features
- Supplier Evaluation and Selection: Choose the right suppliers based on performance history and quality standards, ensuring a reliable supply of materials.
- Real-time Monitoring: Track supplier performance and product quality in real-time, allowing for swift action when issues arise.
- Quality Audits: Streamline the auditing process, ensuring that suppliers meet your quality requirements.
- Document Control: Manage and organize quality documents, certifications, and compliance data to streamline regulatory requirements.
- Risk Management: Identify and mitigate potential risks within your supply chain to prevent quality issues before they occur.
Benefits of Zometric's Supplier Quality Management Software
- Enhanced Product Quality: With real-time monitoring and stringent quality control, your products will meet and exceed industry standards, leading to increased customer satisfaction.
- Cost Reduction: Identifying and addressing quality issues at the source reduces costs associated with rework, returns, and warranty claims.
- Improved Supplier Relationships: Streamlined communication and collaboration with your suppliers lead to stronger, more productive relationships.
- Regulatory Compliance: Ensure that your supply chain adheres to industry regulations and standards, mitigating compliance-related risks.
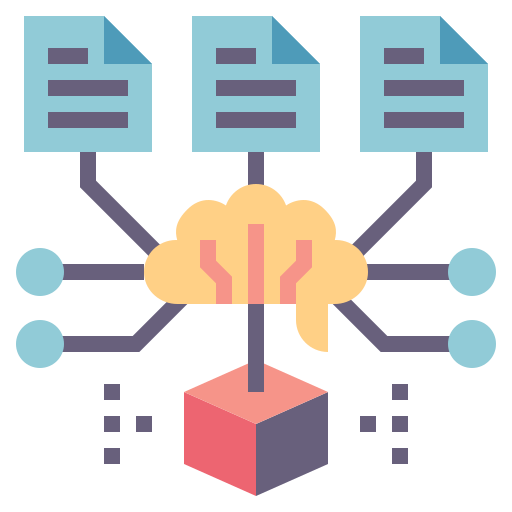
Supplier Quality Management (SQM) System
Quality control begins at the source – your suppliers. In the manufacturing world, having a robust Supplier Quality Management (SQM) system in place is essential. It's not just about ensuring the quality of the end product but also minimizing defects, reducing costs, and maintaining compliance with industry standards.
At Zometric, we understand the significance of a flawless supply chain and impeccable quality. That's why we've developed a comprehensive Supplier Quality Management Software designed specifically for the manufacturing industry.
Elevating Manufacturing Excellence with Zometric's Supplier Quality Management Software Modules.
Modules of Supplier Quality Management Software
Supplier Evaluation and Selection:
Supplier Onboarding
Streamlines the process of adding new suppliers to your network.
Supplier Performance Metrics
Tracks and evaluates supplier performance based on various key performance indicators (KPIs).
Supplier Risk Assessment
Identifies and assesses risks associated with each supplier, helping in risk mitigation.
Quality Audits
Audit Planning
Schedules and plans supplier audits, specifying criteria and requirements.
Audit Execution
Conducts on-site or remote audits to evaluate supplier compliance with quality standards.
Audit Reporting
Generates comprehensive reports with audit findings and corrective actions.
Real-time Monitoring
Quality Data Capture
Collects real-time quality data from suppliers, enabling immediate visibility into product quality.
Alerts and Notifications
Provides alerts for quality deviations or non-conformance, allowing for quick response and resolution.
Document Control
Document Repository
Manages and organizes quality-related documents, such as certifications, test reports, and compliance data.
Document Version Control
Ensures that the most up-to-date quality documents are readily available.
Non-Conformance Management
Non-Conformance Reporting
Allows the reporting of quality issues and discrepancies.
Corrective and Preventive Actions (CAPA)
Tracks and manages actions taken to address non-conformance issues.
Supplier Collaboration
Communication Tools
Provides tools for efficient communication and collaboration with suppliers.
Supplier Portal
Allows suppliers to submit quality data and documents directly, improving transparency and collaboration.
Quality Data Analytics
Data Analysis Tools
Offers data analytics and reporting features to identify trends, performance improvements, and areas for optimization.
Quality Metrics and Dashboards
Presents key quality metrics in a visual format for easy analysis.
Regulatory Compliance
Compliance Tracking
Ensures that suppliers adhere to industry-specific regulations and standards.
Regulatory Reporting
Generates reports and documentation required for compliance purposes.
Zometric is the preferred choice for manufacturing software requirements. Our Supplier Quality Management Software Solutions empower manufacturers to excel in today's competitive environment. Contact us today to learn more about how our software solutions can revolutionize your manufacturing operations.
In today's competitive manufacturing environment, quality is the cornerstone of success. Zometric's Supplier Quality Management Software empowers manufacturers to maintain the highest standards in their supply chain, ensuring top-notch product quality and long-lasting customer satisfaction.
Use case of Supplier Quality Management Software
Supplier Quality Management Software (SQM Software) plays a vital role in the manufacturing industry by helping businesses ensure the quality and reliability of materials and components sourced from suppliers. Here are some key use cases for Supplier Quality Management Software in manufacturing:
SQM software helps manufacturers assess and select the right suppliers based on their performance history, quality standards, and compliance with industry regulations. This use case ensures that manufacturers work with reliable and quality-focused suppliers.
Manufacturers can use the software to capture quality data in real-time, both on-site and remotely, during the manufacturing process. This enables them to monitor and verify the quality of materials and components as they are being produced, reducing the risk of defects and non-conformance.
SQM software allows manufacturers to plan and conduct supplier audits to evaluate compliance with quality standards. This use case ensures that suppliers meet specific requirements and maintain consistent quality levels.
When quality issues or non-conformance instances are identified, the software helps manage the reporting, investigation, and corrective actions required to address these issues promptly. This ensures that defects and quality problems are addressed effectively.
SQM software manages and organizes quality-related documents, including certifications, test reports, and compliance data. This use case ensures that the right documentation is readily available and up-to-date.
Effective communication and collaboration with suppliers are essential for quality management. The software often includes communication tools and supplier portals to facilitate the exchange of information, data, and feedback.
Manufacturers use SRM features to maintain a positive and productive relationship with suppliers. Supplier scorecards and feedback mechanisms help identify areas for improvement and foster collaboration.
Manufacturers can assess and monitor potential risks in their supply chain. This use case helps identify and mitigate risks early, reducing the likelihood of quality problems and disruptions.
SQM software provides data analytics and reporting tools to analyze supplier performance, identify trends, and make data-driven decisions to enhance quality.
Ensuring compliance with industry-specific regulations and standards is crucial in manufacturing. The software tracks and documents compliance to meet regulatory requirements.
SQM software assists manufacturers in identifying opportunities for process improvement and optimizing supplier relationships. This use case leads to ongoing quality enhancement and cost reduction.
Integration with other systems, such as ERP and supply chain management software, streamlines data exchange and ensures data continuity throughout the organization's operations.
Schedule a free Demo
Connect with Us for a Demo and Pricing Inquiry
Easy-to-integrate Modules
Never before has software customization been so easy!
Seamlessly Integrate Modules with Zometric's Supplier Quality Management Software
At Zometric, we understand that every manufacturing operation is unique, and that's why we've designed our Supplier Quality Management Software to be as flexible as your business demands. With easy-to-integrate modules, customization has never been this simple. Connect with us to discover how Zometric's modular approach empowers you to tailor your software to your precise needs.
Supplier Quality Management software is a versatile tool that can be tailored to the specific needs of a manufacturing or production-oriented business. It plays a critical role in optimizing operations, improving efficiency, and ultimately increasing the competitiveness of a company in the market.
Few of our customers
All About Supplier Quality Management Software FAQs
Supplier Quality Management Software is a specialized tool used in manufacturing to assess, monitor, and manage the quality of materials and components sourced from suppliers. It is crucial for ensuring that the materials meet specific quality standards, which is essential for the overall quality of the final products.
SQM Software allows manufacturers to evaluate potential suppliers based on their performance history, quality metrics, compliance with industry regulations, and other criteria. It aids in the selection of reliable and quality-focused suppliers.
Real-time monitoring involves capturing quality data during the production process in real time. It helps manufacturers monitor and verify the quality of materials and components as they are produced. This ensures that defects and non-conformance are detected and addressed promptly, reducing the risk of subpar products.
SQM Software supports the planning, execution, and reporting of supplier audits. This allows manufacturers to evaluate supplier compliance with quality standards and identify areas for improvement, ultimately ensuring consistent quality levels.
Non-conformance management in SQM Software involves reporting and managing quality issues and discrepancies. It ensures that when quality problems are identified, they are investigated, documented, and corrective actions are taken to address the issues, preventing recurrence.
Document control in SQM Software manages and organizes quality-related documents, such as certifications, test reports, and compliance data. It ensures that the right documentation is readily available and up-to-date for audits and regulatory compliance.
Supplier collaboration features in SQM Software facilitate effective communication and collaboration between manufacturers and suppliers. It includes tools and portals for exchanging information, data, and feedback, enhancing transparency and cooperation.
SRM features in SQM Software help manufacturers maintain productive relationships with their suppliers. Supplier scorecards and feedback mechanisms provide insights into supplier performance and areas for improvement.
SQM Software supports the identification and assessment of potential risks in the supply chain. By monitoring these risks, manufacturers can take proactive measures to reduce the likelihood of quality problems and disruptions.
SQM Software provides data analytics and reporting tools to analyze supplier performance and identify trends. This enables manufacturers to make data-driven decisions for process improvement, ultimately leading to enhanced product quality and cost reduction.
Yes, SQM Software solutions offer integration capabilities, allowing seamless data exchange with other systems such as ERP (Enterprise Resource Planning) and supply chain management software to ensure data continuity across the organization.
You can call Zomtric Technical team to help you address all your needs/ requirement.
To get started with implementing SQM Software, we understand your need and suggest software solution that aligns with your company's needs and goals. We specializes in SQM solutions and offers support for successful implementation.
Table of Contents
- 1 Supplier Quality Management Software Solutions
- 2 Why Choose Zometric's Supplier Quality Management Software?
- 3 Elevating Manufacturing Excellence with Zometric's Supplier Quality Management Software Modules.
- 4 Modules of Supplier Quality Management Software
- 5 Use case of Supplier Quality Management Software
- 6 Easy-to-integrate Modules
- 7 Few of our customers